УСОВЕРШЕНСТВОВАНИЕ СХЕМЫ ПЫЛЕПРИГОТОВЛЕНИЯ С ПРОМЕЖУТОЧНЫМИ БУНКЕРАМИ И СЖИГАНИЯ ПЫЛИ ПОДМОСКОВНОГО УГЛЯ В ГОДЫ ОТЕЧЕСТВЕННОЙ ВОЙНЫ И В ПОСЛЕВОЕННЫЙ ПЕРИОД
Глава книги "Мосэнерго за 40 лет" под редакцией М.Я. Уфаева, А.П. Немова, Я. М. Островского и Г. С. Сафразбекяна 1958 года выпуска.
В период Отечественной войны, когда поступление донецкого угля в Центральный район было отрезано, московские ТЭЦ № 7, 8, 9 и 11 были переведены с донецкого угля на подмосковный.
На ТЭЦ № 7 предварительная сушка подмосковного угля производилась в центральной трубе-сушилке дымовыми газами по разомкнутому циклу. Газы для сушки отбирались из работающих котлов и, пройдя трубу-сушилку и два последовательно установленных циклона, удалялись в атмосферу. Эффективность циклонов была низкой, и выброс угля атмосферу значителен. Сушонка поступала установленные у котлов мельницы «Резолютор». Вследствие недостаточной производительности мельниц при работе на подмосковном угле производительность котлов снизилась с 23 до 13 т/ч.
На ТЭЦ № 8 на имевшихся в то время двух пылеугольных котлах среднего давления мельницами «Резолютор» сушка угля производилась в индивидуальных трубах-сушилках замкнутому циклу. Котлы работали по тому времени удовлетворительно. На ТЭЦ № 9 котлы были оборудованы одновентиляторными мельничными системами с барабанно-шаровыми мельницами. Недостаточный напор вентилятора затруднял перемешение трубы-сушилки, имеющей значительное сопротивление из-за большой скорости восходящего потока газов и затраты тяги на подъем угля. Кроме того, в стесненных условиях ТЭЦ № 9 возникли трудности с размещением под трубой-сушилкой колчеданного мешка, куда выпадают колчедан и наиболее крупные куски угля, и с удалением их. Поэтому была сделана попытка организовать предварительную сушку подмосковного угля на нисходящем участке подвода газа к мельнице. Это решение дало положительные результаты. Таким образом, было разбито господствовавшее до того времени представление, что эффективная подсушка влажного угля происходит только при восходящем потоке горячих газов. Так, развитие схемы предварительной сушки подмосковного угля во взвешенном состоянии привело к отказу от предварительной подсушки угля в трубах-сушилках.
Конструктивная схема сушки угля, в нисходящем потоке практически не отличается от сушки в одной мельнице, поскольку выполнение нисходящего участка газохода высотой 2,5—4 м не вызывает каких-либо осложнений.
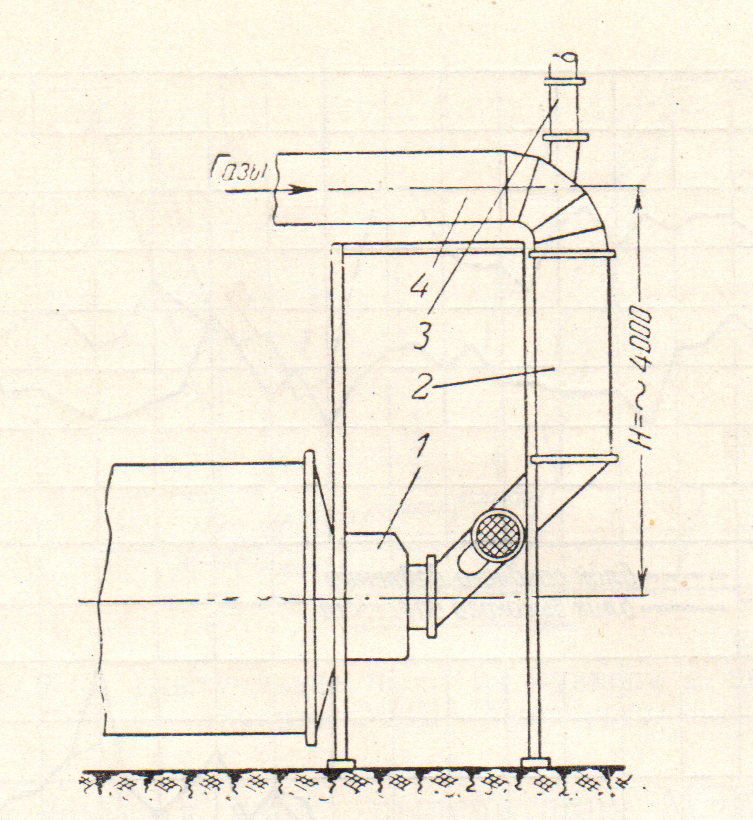
Мельничная установка с предварительной подсушкой угля в нисходящем потоке газов.
При сушке подмосковного угля в нисходящем участке колчедан не сепарируется. Так как в трубе-сушилке сепарируется не более 10 —15% от всего количества топлива, то ликвидация сепарации колчедана в таком размере существенно не сказывается на изменении условий работы мельниц и топок. Схема подсушки в нисходящем потоке газов обеспечивает практически ту же производительность мельничной установки, что и двухвентиляторная схема. Опыт ТЭЦ № 9 по сушке в нисходящем потоке через непродолжительный срок нашел широкое распространение как при размоле подмосковного угля (ТЭЦ ЗИЛ, ТЭЦ № 15 Мосэнерго, Сталиногорская ГРЭС и др.),так и других бурых углей.
На ТЭЦ № 9 одновентиляторная мельничная система с сушкой в нисходящем потоке давала производительность порядка 27 т/ч, что не обеспечивало полной нагрузки котлов. На котлах, в особенности на котле № 1, имело место значительное шлакование топок. В связи с неприспособленностью мельниц и топок для размола и сжигания подмосковного угля и низких показателей работы ТЭЦ № 7, 8 и 9 в 1945—1946 гг. были вновь переведены на работу на донецком тощем угле.
Проект ТЭЦ № 11 предусматривал работу электростанции на подмосковном угле. Пылеприготовление было выполнено на двух котлах по трехвентиляторной схеме и на третьем котле по двухвентиляторной. Поэтому перевод ТЭЦ № 11 с донецкого угля на подмосковный не требовал сложных конструктивных решений. Особенностью трехвентиляторной схемы пылеприготовления на ТЭЦ № 11 является использование дымовых газов для сушки угля не только в трубе-сушилке, но и в мельнице. Интенсификация сушки в мельнице позволила довести производительность сушильно-мельничной системы в эксплуатационных условиях до 50—55 т/ч и нагрузку котла до 175 т/ч при работе одной системы.
Динамика углубления пыли и удельного расхода электроэнергии на пылеприготовление по Сталиногорской ГРЭС.
R200—остаток на сите 200 мк;
Э—удельный расход электроэнергии на пылеприготовление.
На ТЭЦ № 11 в условиях военного и послевоенного времени была проделана серьезная работа по наладке режимов работы пылеприготовительного оборудования и котлов на подмосковном угле. Несмотря на достигнутые удовлетворительные показатели, в целях уменьшения загрязнения атмосферного воздуха Москвы золой и сернистыми газами котлы ТЭЦ № 11 в 1953—1954 гг. были переведены на сжигание донецкого тощего угля. При восстановлении Сталиногорской ГРЭС основное оборудование в значительной мере было установлено новое, число котлов увеличено до 12 и мощность электростанции превзошла довоенную. При восстановлении электростанции учитывался накопленный опыт размола и сжигания подмосковного угля. Пылеприготовление выполнялось по двухвентиляторной схеме, а затем и по одновентиляторной схеме с сушкой в нисходящем потоке. Топки котлов полностью экранировались с малым шагом труб, с устройством холодных воронок. Так как часть новых котлов особых поставок (№ 2—5) поступила с шагом экранных труб 140 мм при диаметре труб 70 мм, то Мосэнергопроектом были разработаны, а Центральным ремонтно-механическим заводом Мосэнерго изготовлены и смонтированы развилки экранных труб, позволившие уменьшить шаг труб до 93 мм. Установка развилок на котлах Сталиногорской ГРЭС с давлением 110 ати была выполнена впервые. Экраны с развилкой работают надежно. Шлакование топок несколько снизилось. Обеспечение бесшлаковочного режима котлов на Сталиногорской ГРЭС и на других электростанциях, работающих на подмосковном угле, решается наряду с полным экранированием топок путем усовершенствования горелок, организации обдувки экранов паром или перегретой водой и, что очень важно, отладкой режима работы сушильно-мельничных систем, пылепитателей и горелок. Пересушка и тонкий помол пыли приближают момент воспламенения факела и усиливают шлакование топок. На Сталиногорской ГРЭС была проведена работа по угрублению помола пыли и ликвидации случаев пересушки ее. Для угрубления помола пыли были переделаны мельничные сепараторы; путем изменения давления первичного воздуха по отдельным пылепроводам удалось регулировать положение факела и устанавливать ядро в центре топки. Бесшлаковочная нагрузка котлов повысилась, химическая неполнота горения отсутствовала, содержание горючих в уносе осталось на том же уровне 0,5—1%, что и при тонком помоле.
С конца 1948 г. до середины 1951 г. помол пыли был угрублен с остатка 7,5% на сите 200 мк до остатка 11 —12%. В результате угрубления помола и наладки сушильно-мельничных систем расход электроэнергии на пылеприготовление снизился с 18—19 до 15— 16 квт-ч/т угля. Расход шаров снижен до 340—360 г/т угля. На Сталиногорской ГРЭС установлены шнековые пылепитатели. Длительное время проводились исследование и наладка работы пылепитателей для обеспечения одинаковой и устойчивой подачи пыли каждым питателем. Особенно остро выявилась необходимость обеспечения надлежащей работы пылепитателей в связи с автоматизацией процесса горения.
Начиная с 1950 г., с привлечением МЭИ был проведен в несколько этапов комплекс работ по изучению и усовершенствованию конструкции шнекового пылепитателя, а затем и пылевого бункера.Первый этап работ привел к конструкции ступенчатого шнека с допрессовкой пыли, обеспечивающей забор пыли из бункера по всей длине активной части шнека и не допускающей самопроизвольного протекания пыли. В течение 1953—1954 гг. на Сталиногорской ГРЭС и ряде электростанций Мосэнерго (ТЭЦ № 11, 12 и др.) были установлены шнеки новой конструкции, что дало положительные результаты. На одном прямоточном котле высокого давления среднее число и длительность выбега температуры перегретого пара более +10° С снизились в 2—2,5 раза. На барабанном котле число отклонений давления пара более 2 ат сократилось в 2,3 раза.
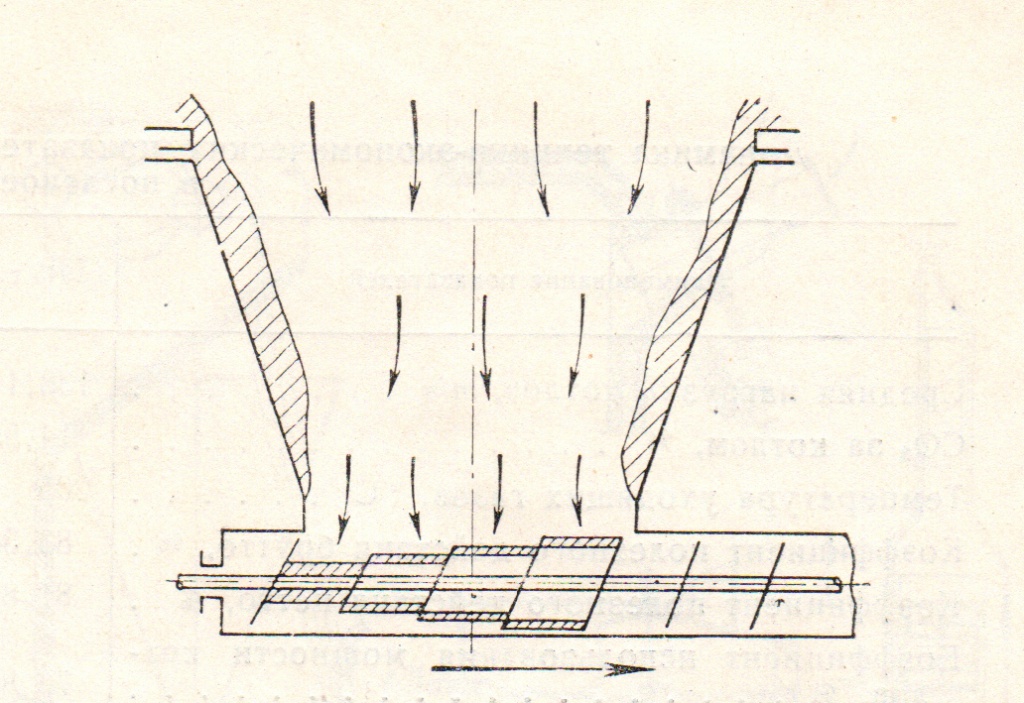
Поступление пыли из бункера в шнек конструкции МЭИ—Мосэнерго.
Кусинский завод, выпускающий шнековые пылепитатели, с 1956 г. приступил к изготовлению модернизированных пылепитателей конструкции МЭИ—Мосэнерго. На втором этапе на основе дальнейшего изучения работы пылевого бункера и пылепитателей пришли к новой конструкции узла пылепитания, предусматривающей выполнение стенок пылевого бункера вертикальными с минимальным сужением в нижней части и соответствующее удлинение активной части ступенчатого шнекового пылепитателя. Новая конструкция узла пылепитания, осуществленная в 1954—1956 гг. на одном котле ТЭЦ № 12 и одном котле Сталиногорской ГРЭС, позволила добиться вполне надежной и стабильной работы автоматики горения и улучшения топочного режима. Новая конструкция узла пылепитания МЭИ—Мосэнерго продолжает внедряться на действующих электростанциях, а также при расширении и сооружении новых электростанций с промежуточными бункерами пыли. При восстановлении Сталиногорской ГРЭС и ТЭЦ № 15 Мосэнерго были также установлены пневматические мельницы конструкции ВТИ. Таких мельниц в системе было установлено шесть, из них четыре на Сталиногорской ГРЭС, по одной на ТЭЦ № 9 и 15.
Производительность пневмомельниц при размоле подмосковного угля была достигнута при испытаниях 35—40 т/ч, удельный расход электроэнергии на размол 16—20 квт-ч/т при остатке на сите 200 мк—10—11%.
Общий вид узла пылепитания конструкции МЭИ—Мосэнерго.
Динамика технико-экономических показателей котельного цеха Сталиногорской ГРЭС
Наименование показателей |
1945 г. |
1950 г. |
1951 г. |
1952 г. |
1953 г. |
1954 г. |
1955 г. |
1956 г. |
Средняя нагрузка котлов, т\ч |
138,1 |
157,2 |
162,3 |
165,4 |
163,5 |
166,8 |
166,2 |
164,1 |
СО2 за котлом, % |
14,55 |
14,00 |
13,80 |
14,11 |
14,18 |
14,0 |
13,90 |
13,4 |
Температура уходящих газов, оС |
205 |
186 |
183 |
184 |
173,5 |
177 |
176 |
177 |
Коэффициент полезного действия брутто, % . |
83,36 |
84,5 |
85,45 |
86,10 |
87,19 |
87,35 |
87,51 |
87,72 |
Коэффициент полезного действия нетто, % . |
81,84 |
80,59 |
82,12 |
83,13 |
84,30 |
85,02 |
85,40 |
86,16 |
Коэффициент использования мощности котлов |
76,82 |
61,7 |
64,5 |
66,7 |
66,3 |
70,2 |
62,8 |
56,0 |
Производительность сушильно-мельннчных систем,т\ч |
27,3 |
3~,64 |
35,35 |
35,72 |
35,62 |
35,25 |
34,68 |
34,9 |
Удельный расход электроэнергии на пылеприготовление, квт.ч\т |
18,85 |
16,56 |
16,26 |
15,84 |
14,51 |
12,93 |
13,22 |
13,25 |
Эксплуатация пневмомельниц выявила ряд существенных недостатков и в первую очередь сквозной износ отдельных элементов с толщиной стенки 50—70 мм (разгонного аппарата и диффузора) в течение 800—1 000 ч работы, что резко, ухудшало технико-экономические показатели мельниц и требовало частого капитального ремонта. Пересушка пыли до влажности 8—12% и большие выходные скорости в горелках по первичному воздуху вызывали сильное шлакование топки. Для удаления отходов выпадающих в колчеданные мешки пневмомельниц колчедана и крупных кусочков угля требовался дополнительный персонал. По этим причинам большинство пневмомельниц демонтировано и осталось по одной пневмомельнице на Сталиногорской ГРЭС и ТЭЦ № 15 Мосэнерго.
В результате освоения и усовершенствования нового оборудования, устранения многочисленных недоделок и дефектов монтажа и повышения уровня эксплуатации технико-экономические показатели Сталиногорской ГРЭС по пылеприготовлению и сжиганию подмосковного угля в последние годы улучшились и значительно выше довоенных. На Сталиногорской ГРЭС имеются еще значительные резервы по улучшению топливо-использования в котельной за счет улучшения топочного режима, а также снижения потери тепла с уходящими газами.
При проектировании ТЭЦ № 17 была применена для котлов № 1 и 2 производительностью до 100 т/ч схема пылеприготовления, по которой газы с испаренной из угля влагой после мельницы направляются в топку через сбросные горелки. Транспорт пыли к основным рабочим горелкам производится горячим воздухом. В эксплуатации достигнута производительность мельниц 50 т/ч. Топки работают устойчиво без мазута при нагрузке котла до 25% от номинальной. Однако в условиях ТЭЦ № 17 вследствие необходимости частых остановок мельниц и низкого перегрева пара из-за недостаточной поверхности нагрева пароперегревателей эта схема пылеприготовления не дала должного эффекта. По этой причине, а также вследствие перехода к применению на вновь устанавливаемых котлах на подмосковном угле шахтных мельниц схема пылеприготовления с подачей пыли горячим воздухом нашли в дальнейшем распространение только при сжигании каменных углей и антрацита с малым выходом летучих.
Последней установкой, на которой применены схема пылеприготовления с промежуточными бункерами и барабанно-шаровые мельницы для подмосковного угля, является Черепетская ГРЭС. При проектировании в 1949-1950 гг. котлов на сверх высокие параметры пара для Черепетской ГРЭС Таганрогский котельный завод отказался от применения шахтно-мельничных топок, считая нецелесообразным накладывать на процесс освоения сверхвысоких параметров также освоения шахтно- мельничных топок, которые к тому времени еще не были в достаточной мере освоены и отладены на эксплуатируемых котлах. Принятая схема пылеприготовления с промежуточными бункерами пыли, несмотря на длительный опыт ее эксплуатации и учет в значительной мере этого опыта при конструировании котельного агрегата, не исключила значительных трудностей в освоении и наладке сжигания подмосковного угля на Черепетской ГРЭС. Топочная камера котла ТП-240-1 имеет объем 1 400 м3 и сечение в плане 10,7X7,3 м2. Все стенки топки экранированы трубами диаметром 60 мм с шагом 81 мм. Тепловое напряжение топки 133 тыс. ккал/м3 • ч при номинальной нагрузке котла 240 т/ч. Восемь поворотных горелок прямоточного типа размещены в углах, на боковых стенах топки, в два ряда с пересечением факелов в центре топки. Поворот горелки возможен в вертикальной плоскости на 12о вверх и 20° вниз. Расчетные скорости воздуха: первичного 35 м/сек и вторичного 37 м/сек. Над рабочими горелками установлены четыре горелки сбросного воздуха и четыре горелки третичного воздуха. Котельный агрегат оборудован двумя одновентиляторными сушильно-мельничными системами с сушкой в нисходящем потоке газов, с барабанно-шаровыми мельницами типа 287/470 и мельничными вентиляторами производительностью по 90 тыс. м3/ч и напором 950 мм вод. ст.
Своеобразие освоения сжигания подмосковного угля на Черепетской ГРЭС, помимо новизны отдельных конструктивных решений, заключается в том, что вследствие поставки угля с разных месторождений Подмосковного бассейна, начатых разработкой большей частью в последние годы, качество поставляемого угля очень переменное и значительно более низкое, чем на других электростанциях. Зольность на сухую массу отдельных партий угля колеблется в пределах 28—54%, влажность достигает 37%, теплотворная способность меняется от 1 650 до 2 900 ккал/кг. Температура начала деформации золы составляет от 1000 до 1500° С.
Основной трудностью, выявившейся в эксплуатации, явилось шлакование топки, главным образом фронтового и заднего экранов, скатов холодной воронки и газоотборных окон. В условиях недостаточной циркуляции шлакование вызывало неоднократные разрывы труб, главным образом фронтового экрана. Нагрузка котлов ограничивалась шлакованием экранов и составляла первоначально 170— 180 т/ч. Основными причинами шлаковки явились неудовлетворительная конструкция угловых горелок в сочетании с вытянутой формой топки, отсутствие обдувочных устройств, наличие не защищенных экранами участков кладки у муфельных горелок и кирпичной разделительной стенки между шлаковыми комодами тепла с уходящими газами повышенные присосы воздуха в топку через шлаковые комоды вследствие значительного времени на удаление шлака. Для устранения шлаковки в процессе эксплуатации установленных и монтажа последующих агрегатов были внесены конструктивные изменения в отдельные элементы, испытаны и отработаны различные режимы топочного процесса. Кирпичные разделительные стенки между шлаковыми комодами и муфельные горелки удалены. Проверены различные конструкции горелок и схемы их установки.
Топочная камера котла ТП-240-1 Черепетской ГРЭС.
Сбросные горелки установлены на фронтовой и задней стенах топки на уровне рабочих горелок с направлением осей к центру топки. Для обдувки экранов в каждой топке установлено от 9 до 12 паровых обдувочных аппаратов типа ОПР-5 завода Ильмарине. Проведенные мероприятия позволили довести нагрузку котлов до номинальной — 240 т/ч — и улучшить технико-экономические показатели работы котельных агрегатов. Однако работу топок в настоящее время еще нельзя считать полностью налаженной как в части ликвидации шлакования экранов, так и уровня экономичности. Работа в этом направлении продолжается. На котле № 1 в капитальный ремонт 1957 г. установлена опытная конструкция непрерывного шлакоудаления. Устраняется присадка холодного воздуха к мельничным вентиляторам неработающих мельниц и проводятся другие мероприятия.
В 1957 г. выявлена наружная коррозия экранных труб холодной воронки, в особенности на первых двух котлах. По предварительным данным коррозия вызвана действием серы топлива на металл труб при повышенной температуре. Не исключено и механическое воздействие шлака и пылевого факела на износ труб. Для изучения этого явления и выработки необходимых мероприятий по предупреждению в дальнейшем коррозии экранных труб проводятся необходимые исследования и наблюдения с привлечением работников научно-исследовательских институтов. Перед коллективом Черепетской ГРЭС стоит задача повышения культуры эксплуатации и ремонта оборудования и дальнейшего улучшения показателей использования многозольного, низкокалорийного подмосковного угля.
Схемы установки горелок в топке, испытанные на Черепетской ГРЭС.
1—диагональная;
2—блочная с фокусами на большой оси топки;
3—блочная с фокусами на малой оси топки;
4—тангенциальная.
Горелки с шамотным рассекателем на котлах № 1, 2, 4 и 5 Черепетской ГРЭС.
Освоение сжигания подмосковного угля в шахтно-мельничных топках.
Достигнутый прогресс в подсушке угля в мельницах в процессе размола и в сжигании пыли угрубленного помола позволил пойти на опробование в эксплуатационных условиях на крупных котельных агрегатах нового способа организации сушки, размола и сжигания подмосковного угля — шахтно-мельничной топки. Основными достоинствами шахтно-мельничных топок по сравнению со схемой пылеприготовления с промежуточными бункерами являются значительное снижение капитальных затрат", упрощение обслуживания и снижение расхода электроэнергии на пылеприготовление.Шахтно-мельничные топки, как известно, начали применяться в СССР еще в довоенный период для котлов малой и.' средней мощности при работе на торфе и сланцах. На крупных котлах шахтно-мельничные топки впервые применены для котлов высокого дав-ия ТП 230. Головной котел с шахтно-мельничной топкой вошел в эксплуатацию на ТЭЦ №15 Мосэнерго в 1948 г. На котле установлены четыре мельницы типа ШМА-730-1660-2004. Расположение мельниц — по фронту котла.
Задача освоения шахтно-мельничных топок заключалась в первую очередь в отработке надежной конструкции мельницы и организации надлежащей аэродинамики факела в топке, обеспечивающей надежную работу отдельных элементов котла—экранов и пароперегревателей Наряду с этим надлежало добиться наилучших экономических показателей по расходу электроэнергии на размол, по повышению экономичности работы котельного агрегата. В значительной мере эти вопросы решались на ТЭЦ № 15. Первоначальная конструкция мельниц, установленных на ТЭЦ № 15, имела многочисленные недостатки. В первый период эксплуатации неоднократно происходили поломки корпуса подшипника и прогиб вала вследствие сильной вибрации опорной рамы заднего подшипника. Пришлось переделать фундаменты под подшипниками и увеличить их массу, усилить жесткость крепления рам. Отсутствие компенсаторов и футеровки верхней части приводили к короблению стенок шахт, к разрыву листов по сварке, к неплотности шахт и пылению. Оказалось, необходимым установить линзовые компенсаторы между мельницей и шахтой, а также шахтой и обшивкой котла, сделать футеровку верхней части шахт и коробов горячего воздуха. Быстрый износ брони и бил требовал частого ремонта мельниц. Путем подбора материала и толщины брони, организации наплавки бил и внедрения комбинированных бил срок службы брони был увеличен с 3 до 9 мес, бил средних рядов — с 220—250 до 500—600 ч и бил крайних рядов — со 100— 120 до 250—300 ч. Были выявлены оптимальное число и расположение бил, что обеспечило устойчивую работу мельниц. При попадании в мельницу вместе с углем металлических предметов повреждаются била и мельница выходит из строя. Поэтому непосредственно перед мельницами были установлены магнитные сепараторы.
Аэродинамика факела в шахтно-мельничной топке первоначально была неудовлетворительной. Большое сечение амбразур (1,56хl,56 м) способствует дальнебойности пыле-воздушного факела и затрудняет смешение со вторичным воздухом. Заполнение топки было неравномерным, и ядро факела располагалось у задней стенки топки это приводило к шлакованию перегревателя. На работу топки отрицательно сказывалось поступление больших количеств неорганизованного холодного воздуха через неплотности холодной воронки, топливоподающего узла мельниц и амбразуры неработающей мельницы. Для улучшения топочного процесса были опробованы различные конструкции шлиц вторичного воздуха и вставки в амбразурах и выполнен дополнительный подвод воздуха в топку через заднюю стенку. Были уплотнены холодные воронки, реконструирован и герметизирован узел подачи угля в мельницу. Установлены шиберы для отключения шахт неработающих мельниц. Проведение указанных мероприятий и установка эжекционных горелок по опыту второй очереди Щекинской ГРЭС улучшили работу топок и обеспечили надежную работу котлов.
Технико-экономические показатели котлов № 3, 4 и 5 ТЭЦ № 15 Мосэнерго, оборудованных шахтно-мельничными топками, первоначально были ниже, чем у аналогичных котлов с барабанно-шаровыми мельницами, вследствие более высокого содержания горючих в уносе — 2—2,5%. По мере усовершенствования конструкции оборудования и наладки режимов работы технико-экономические показатели этих котлов непрерывно улучшались.
На ТЭЦ № 17, начиная с 1953 г., установлено пять котлов ТП-230 с шахтно-мельничными топками, аналогичных котлам ТЭЦ № 15. В конструкции и в эксплуатации шахтно-мельничных топок на ТЭЦ № 17 учтен опыт работы котлов на ТЭЦ № 15. Технико-экономические показатели котлов на ТЭЦ № 17 несколько ниже, чем на ТЭЦ № 15, как вследствие недостаточной освоенности оптимальных режимов работы котлов, так и недостатков в постановке учета топлива и выработки пара котлами.
На ТЭЦ № 15 и 17 имеются возможности для значительного улучшения технико-экономических показателей работы котлов. Это подтверждается результатами работы котлов Щекинской ГРЭС, также оборудованных шахтно-мельничными топками.
Встроенный жалюзийный золоуловитель.
В 1950 г. вступили в строй первые агрегаты Щекинской конвективной шахте, в особенности трубы водяных экономайзеров. Интенсивность износа зависит главным образом от концентрации летучей золы в дымовых газах и скорости газоз. Борьба с золовым износом ведется по двум направлениям — снижение концентрации золы и уменьшение скорости газов. Уменьшение концентрации золы в потоке газов достигается путем установки встроенных в конвективный газоход жалюзийных золоуловителей системы ВТИ — Мосэнерго.
Конструкция встроенных жалюзийных золоуловителей обусловлена температурой газов в месте установки. При температуре газов 500—600° С установлены неохлаждаемые золоуловители из чугуна или даже углеродистой стали. При температуре газов 700—800°С установлены золоуловители с воздушным охлаждением колосников или с колосниками из хромистой стали. Коэффициент полезного действия встроенных золоуловителей составляет от 20 до 35% в зависимости от сопротивления решетки. Улавливая наиболее грубую, абразивную фракцию золы, встроенные жалюзийные золоуловители обеспечивают резкое сокращение износа последующих поверхностей нагрева. Встроенные жалюзийные золоуловители установлены на пяти котлах Сталиногорской ГРЭС, пяти котлах ТЭЦ № 15 и одном котле ТЭЦ № 17, всего на 11 котлах. Встроенные жалюзийные золоуловители имеют сопротивление от 15 до 40 мм вод. ст., что вызывает увеличение расхода электроэнергии на дымососы. Вследствие пропуска до 10% газов мимо водяного экономайзера и потери тепла с физическим теплом горячей золы, КПД котлов снижается на 0,5— 1%. Поэтому встроенные жалюзийные золоуловители нашли только ограниченное применение. На первых котлах ТП-230 скорость газов в экономайзере доходила до 15 м/сек. В связи с интенсивным золовым износом при таких скоростях газов на котлах второй очереди Щекинской ГРЭС и Черепетской ГРЭС скорость газов снижена до 8—9 м/сек. При этом интенсивность износа уменьшилась в несколько раз.
Количество вынужденных остановок котлов по причине золового износа.
Разработаны проекты увеличения сечения газоходов и на действующих котлах, которые будут осуществляться в ближайшие годы. Наряду с указанными главными направлениями по борьбе с золовым износом ведется профилактическая работа в виде установки защитных манжет периодического поворачивания и замены изношенных змеевиков. В результате проводимых мероприятий число случаев вынужденных остановок котлов из-за золового износа систематически снижается, несмотря на рост количества установленных котлов.
Средняя зольность и влажность на рабочую массу подмосковного угля, сжигаемого на электростанциях Мосэнерго