ОСВОЕНИЕ КОТЕЛЬНОГО ОБОРУДОВАНИЯ
Быстрые темпы ввода котельных агрегатов высокого давления и главным образом головных образцов отечественного изготовления вызывали в начальный период эксплуатации ряд серьезных трудностей. Длительность рабочей кампании вновь пускаемых котлов нередко составляла первоначально всего лишь несколько суток. Как правило, вынужденные остановы котлов происходили из-за повреждения поверхностей нагрева котельных агрегатов и неисправности котельной арматуры. Простой котлов в различные рода ремонтах доходил до 40% времени.
Наибольшие трудности встретились из-за повреждений труб водяных экономайзеров, составлявших примерно половину от общего числа повреждений поверхностей нагрева кот-лоагрегатов. В основном повреждения водяных экономайзеров сводились к образованию свищей в сварных стыках (50%) и к золовому износу труб (до 30%). Появление свищей в сварных стыках из-за неудовлетворительного качества сварки было ликвидировано путем повышения квалификации сварщиков, улучшения технологии сварки и усиления контроля за проведением сварных работ на поверхности нагрева.
Повреждения труб экономайзеров из-за эолового износа было особенно характерным для котлов ТП-230-1 ТЭЦ № 15, работающих на подмосковном угле с повышенной зольностью при высокой скорости газов в конвективной части. Повреждения водяных экономайзеров из-за золового износа были резко сокращены путем установки встроенных жалюзийных золоуловителей перед водяными экономайзерами этих котлов, а также улучшения контроля за износом труб и состоянием эоловой защиты на котлах, работающих на многозольном топливе.
На котлах первой очереди Щекинской ГРЭС происходили разрывы отводящих труб водяных экономайзеров, расположенных перед пароперегревателем в потоке дымовых газов с температурой порядка 1 000° С. Для предупреждения перегрева и разрыва этих труб их количество сокращено вдвое путем установки собирательных развилок. Наряду с этим было усилено наблюдение за равномерностью питания котлов, в особенности при растопках. После проведения этих мероприятий отводящие трубы водяных экономайзеров длительно работают без повреждений.
Одной из существенных причин вынужденных остановов котлов явились повреждения экранных труб из-за нарушений циркуляции, подшламовой коррозии, износа труб пылевым потоком горелок, дефектов труб и сварных стыков. Нарушения циркуляции и разрывы труб по этой причине происходили на котлах ТП-230 и в особенности на котлах ТП-240 Черепетской ГРЭС. На котлах ТП-230 случаи разрыва труб из-за нарушения циркуляции ликвидированы за счет реконструкции циркуляционного контура и улучшения аэродинамики путем установки эжекционных вставок в амбразуры топок. Для предупреждения обрывов крепления экранных труб вследствие недостаточной температурной компенсации была переделана обмуровка нижней части холодной воронки.
На этих же котлах была переделана заводская конструкция свода топки с выполнением его из огнеупорного бетона и с переделкой конфигурации змеевиков пароперегревателя, что обеспечило длительный срок службы свода.
На пяти котлах Черепетской ГРЭС с момента пуска по 1956 г. было 25 случаев разрыва экранных труб. На этих котлах проведен комплекс мероприятий по повышению надежности циркуляции. Наряду с мероприятиями по снижению шлакования топки был сделан ряд переделок по циркуляционному контуру: переделаны внутрибарабанные устройства переднего барабана для снижения сопротивления парового тракта и устранения понижения- уровня воды в заднем барабане при больших нагрузках котла; переделаны сепарационные устройства в заднем барабане для устранения захвата пара в отпускные турбины, секционированы верхние и нижние коллекторы фронтового экрана для уменьшения влияния неравномерности тепловой нагрузки на циркуляцию и установлены дополнительно шесть отпускных турбин.
Предупреждение шламовой коррозии кипятильников и экранных труб, в особенности наблюдавшейся на котлах первой очереди Щекинской ГРЭС, достигается:
А) снижением выброса в котлы продуктов коррозии из питательного тракта
Б) консервацией котлов во время их стоянки для предохранения металла поверхностей нагрева от коррозии
В) тщательной внутреннее очисткой поверхностей нагрева котлов
Г) деаэрацией питательной воды
Д) исключением вялой циркуляции в трубах, резких и частых теплосмен.
Для предупреждения износа труб пылевым потоком вблизи горелок переделывается разводка труб, устанавливаются индивидуальные защитные манжеты и ведется тщательный осмотр этой зоны труб во время ремонтов.
В начальные период происходили частые остоновы котлов высокого давления из-за разрывов труб пароперегревателей. Одна из причин повреждения пароперегревателей-разбежка температур по змеевикам- ликвидирована путем заделки газовых коридоров, организации перемешивания пара между первой и второй ступенями пароперегревателя и наладкой топочных режимов.
Из-за недостаточной технологической дисциплины и производственной культуры при изготовлении и монтаже пароперегревателей в начальный период внедрения высокого давления (1945—1947 гг.) многие участки змеевиков и штуцера коллекторов пароперегревателей были выполнены из углеродистых труб вместо хромомолибденовых.
При помощи лаборатории металлов ЦРМЗ была проделана кропотливая работа по проверке методом спектрального анализа всех установленных змеевиков и паропроводов, работающих при высокой температуре. После замены выявленных участков из углеродистой стали и организации тщательной предварительной проверки всех изготовленных змеевиков до монтажа, а также и улучшения режима работы,. пароперегреватели котлов высокого давления работают надежно.
На котлах Черепетской ГРЭС возникали трещины в гибах змеевиков третьей ступени пароперегревателя, выполненной из аустенитной стали ЭИ-257. В целях повышения надежности работы перегревателей проведена аустенизация гибов, приняты меры к обеспечению свободного термического расширения труб и разработан метод сухой консервации перегревателей для исключения возможности контакта металла с конденсатом при длительном останове котлов. Появление трещин после выполнения этих мероприятий сократилось и носит в настоящее время случайный характер.
Прямоточные котлы высокого давления имеют незначительное число повреждений поверхности нагрева, главным образом в виде свищей в заводских или монтажных сварных стыках, выполненных недостаточно качественно, и свищей вследствие золового износа. В прямоточных котлах больше, чем в барабанных, подвержены износу падающим шлаком и крупной золой трубы холодной воронки вследствие их горизонтального расположения. На прямоточных котлах приходится менять трубы холодной воронки через 2—3 года вместо 8—10 лет на барабанных котлах при сжигании многозольного топлива.
Достигнутая надежность котлов высокого и сверхвысокого давления характеризуется тем, что за 1956 г. на 57 работавших котлах было 133 случая вынужденных остановок из-за повреждения поверхности нагрева, т. е. в среднем 2,33 случая на котел.
Количество вынужденных остановок по всем котлам, работающим в системе (за исключением находящихся в длительной консервации) систематически снижается, несмотря на увеличение числа котлов. За 1956 г. всего было 198 вынужденных остановок при 128 работающих котлах вместо 326 остановок на 99 котлах за 1951 г. Средняя повреждаемость поверхностей нагрева работающих котлов в системе Мосэнерго за 1956 г. составила 1,55 случая на котел против 2,5—3 случаев по Министерству электростанций в целом за 1955 г.
Другим важным показателем надежности работы котельных агрегатов является длительность непрерывной работы котла. Максимальная длительность непрерывной работы котельного агрегата достигнута на первой очереди Щекинской ГРЭС 66 дней, на второй очереди 53 дня и на Черепетской ГРЭС 93 дня.
Повышение надежности и увеличение межремонтной кампании котлов высокого и сверхвысокого давления сделали возможным в условиях наличия резерва электрической мощности в системе поставить вопрос об отказе от резервных котлов при проектировании новых электростанций и, в частности, отказаться от резервного котла и перейти на блочную схему два котла—турбина на Черепетской ГРЭС.
В свете внедрения блочных схем котел— турбина стоит задача дальнейшего повышения надежности работы котельных агрегатов и увеличения длительности межремонтной кампании. Наряду с улучшением эксплуатации и повышением качества ремонтов необходимо, чтобы заводы-изготовители предусматривали решение задачи повышения надежности работы при конструировании и изготовлении новых котлов.
На основе опыта Мосэнерго можно выдвинуть следующие важнейшие вопросы, разрешение которых обеспечит надежность работы и повышение длительности межремонтной кампании новых котлов:
а) конструкция горелок, их расположение, степень экранирования и установка обдувочных аппаратов должны исключить надобность в остановках котла для расшлаковки;
д) при сжигании сернистых и влажных углей конструкция воздухоподогревателей должна обеспечивать длительную работу без коррозии.
Экономичность работы котлов в значительной мере зависит от температуры уходящих газов. Конструкция большей части котлов, установленных на электростанциях Мосэнерго, была рассчитана на высокую температуру уходящих газов. На котлах Каширской, Шатурской и Сталиногорской ГРЭС были первоначально установлены котлы без водяных экономайзеров. Температура уходящих газов на этих котлах достигала 300° С. Поэтому еще в довоенные годы на них были дополнительно установлены водяные экономайзеры.
Однако и в послевоенные годы температура уходящих газов продолжала оставаться недопустимо высокой. За 1946 г. из 71 установленного котельного агрегата 24 агрегата, т. е. больше одной трети, имели среднегодовую температуру уходящих газов от 200 до 240° С. Коэффициент полезного действия брутто 20 котельных агрегатов составил о 66 до 80'%, 44 агрегатов—до 85% и лишь котельных агрегатов имели к. п. д. 87—90'%.
Начиная с 1946 г., проводилась планомерная работа по снижению температуры уходящих газов на действующих котлах, а в частя вновь устанавливаемых котлов предъявлялись требования к заводам-изготовителям о снижении расчетной температуры уходящих газов.
За период 1946—1956 гг. проведены реконструктивные работы по снижению температуры уходящих газов на значительном количестве котлов. На 17 котельных агрегатах общей паропроизвоительностью 1 750 т/ч произведена переделка хвостовой части с заменой пластинчатых воздухоподогревателей трубчатыми. На 19 агрегатах переделана хвостовая часть котельных агрегатов с установкой малогабаритных воздухоподогревателей и дополнительной поверхности экономайзеров. На шести котельных агрегатах установлены котлы-утилизаторы, экономайзеры низкого давления для подогрева сетевой воды и конденсата турбин. Проведение этих мероприятий, потребовавших значительных капиталовложений, дало и значительное снижение температуры уходящих газов.
Наряду с реконструктивными мероприятиями проводилась работа по снижению температуры уходящих газов за счет обдувки поверхностей нагрева, в первую очередь подверженных шлакованию. За последние 2—3 года внедрена обдувка экранов аппаратами Ильмарине на 35 крупных котлах н намечено оборудовать обдувкой дополнительно не менее чем восемь котлов.
Большое влияние на температуру уходящих газов оказывает степень загрузки воздухоподогревателя воздухом.
Для обеспечения лучшей степени загрузки воздухоподогревателей усилено внимание к вопросу снижения присосов холодного воздуха в мельничных системах и в топку, ликвидации присадки холодного воздуха перед вентиляторами первичного воздуха.
На ряде котельных агрегатов, работающих на подмосковном угле, достигнута среднегодовая температура уходящих газов порядка 140° С, а на газе 120—130° С и КПД брутто котельных агрегатов 89—93%.
|
Температура |
уходящих газов |
, °С | ||
Вид топлива |
1946 г. |
1949 г. |
1952 г. |
1955 г. |
1956 г. |
Подмосковный |
205 |
192 |
182 |
170 |
170 |
Донецкий тощий |
215 |
196 |
189 |
178 |
165 |
торф |
156 |
165 |
165 |
163 |
159 |
мазут-газ |
186 |
192 |
178 |
163 |
165 |
Средняя температура уходящих газов по системе |
192 |
187 |
180 |
168 |
168 |
Снижение температуры уходящих газов: вызвало трудности в связи с забиванием золой и кислотной коррозией поверхностей нагрева. В результате проведенных исследовательских работ и эксплуатационных наблюдений была разработана система мероприятий по защите водяных экономайзеров и воздухоподогревателей от кислотной коррозии. На ГЭС № 1 была повышена температура воды, поступающей в экономайзеры, при помощи пароструйных подогревателей. На 18 котлах, работающих на подмосковном угле, установлены чугунные ребристые воздухоподогреватели. Разработана опытная конструкция горизонтального трубчатого воздухоподогревателя, регенеративного воздухоподогревателя с вращающимися коробами и схема хвостовой части с газовыми испарителями и калориферами (схема ВТИ).
Наряду со снижением температуры уходящих газов проводились мероприятия по снижению содержания горючих в уносе при сжигании тощих углей, по снижению избытков и присосов воздуха. Наиболее крупной работой, проведенной в последние годы, явилась реконструкция топок трех котлов ТЭЦ № 11 под жидкое шлакоудаление, в том числе на двух прямоточных котлах. Перевод этих котлов на жидкое шлакоудаление позволил снизить содержание горючих в уносе до 8— 10% при сжигании полуантрацита с содержанием летучих 5—8%. На барабанном котле № 3 реконструкция топки под жидкое шлакоудаление позволила повысить бесшлаковочную нагрузку котельного агрегата со 180—190 до 230 г/ч. Положительный опыт реконструкции топок котлов № 3—5 дал основание к заказу нового котла № 6 также с топкой для жидкого шлакоудаления.
Снижение присосов воздуха в хвостовой части и в газоходах котельного агрегата достигнуто за счет более качественного уплотнения агрегатов при капитальных и текущих ремонтах, полной или частичной замены изношенных труб воздухоподогревателей. Если в период 1950—1953 гг. около половины всех котельных агрегатов, установленных в системе, имели присосы выше норм, то в настоящее время только пять-шесть котельных агрегатов имеют еще присосы выше нормы.
На отдельных электростанциях, как Щекинская ГРЭС и ТЭЦ № 20, снижены присосы до 50—60% нормы, что указывает на возможность ужесточения действующих норм ПТЭ. Необходимо, однако, чтобы заводы-изготовители при конструировании котельных агрегатов предусматривали надлежащие конструктивные решения, облегчающие поддержание в эксплуатации их высокой воздушной плотности.
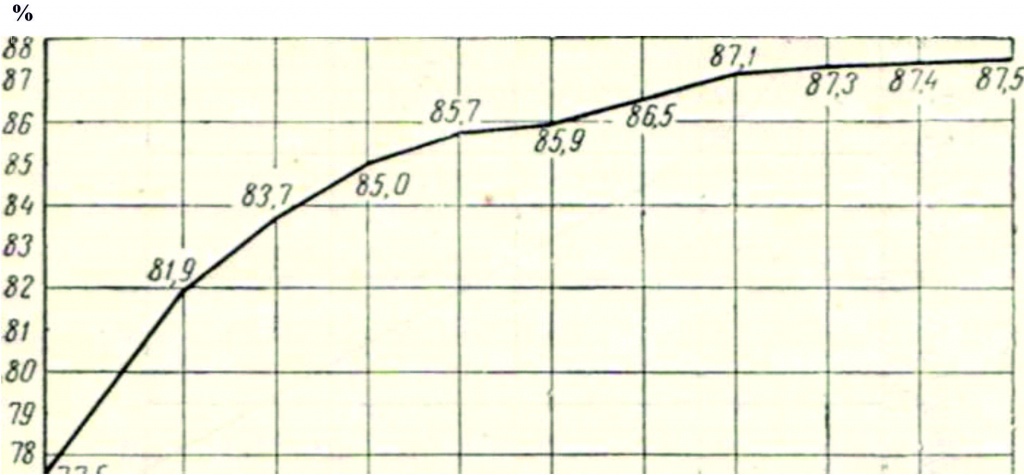
Коэффициент полезного действия котлов брутто по системе.
Подольский завод имени Орджоникидзе за последние годы обеспечил значительное повышение экономичности поставляемых котельных агрегатов (котлы 67СП для Щекин-ской ГРЭС и ТЭЦ № 11). Таганрогский котельный завод вследствие недостаточного учета опыта эксплуатации, в частности опыта Мосэнерго, до последнего времени поставлял котлы с завышенной температурой уходящих газов (котлы ТП-230-2 для ТЭЦ № 17; котлы ТП-240 для Черепетской ГРЭС) и без учета мероприятий по предупреждению коррозии воздухоподогревателей. Опыт Мосэнерго позволяет выдвинуть требование к котельным заводам, чтобы новые котельные агрегаты имели эксплуатационную температуру уходящих газов: при работе на подмосковном угле не выше 140° С; при работе на тощем угле не выше 120°С; при работе на газе не выше 110°С, при отсутствии интенсивной коррозии воздухоподогревателей. Присосы в конвективной шахте не должны превышать 5% от теоретического расхода воздуха. Коэффициент полезного действия брутто котельных агрегатов должен быть в пределах 91—93%.